duction to its aspects such as working principle, structure and application scenarios:
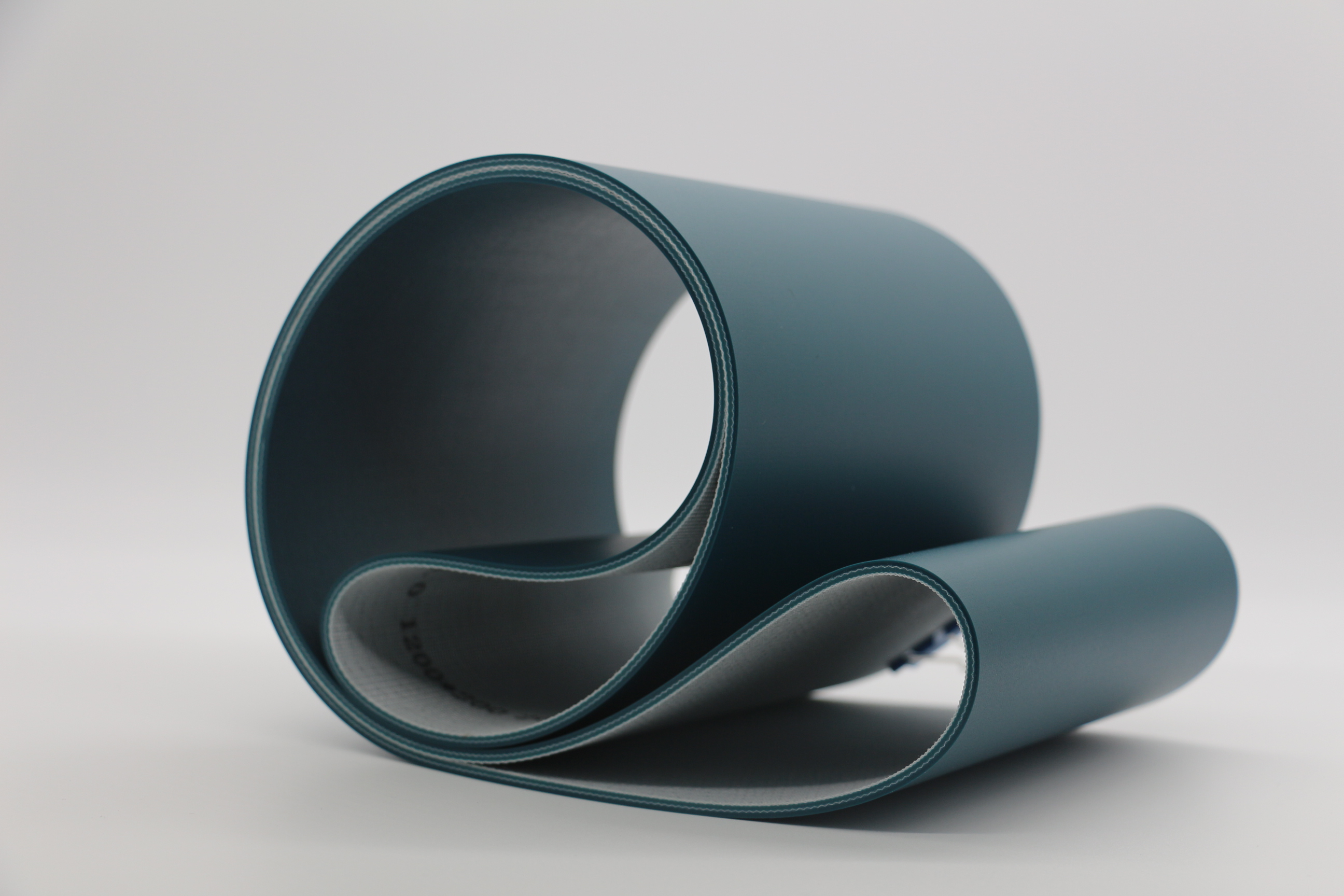
- Scraper Cleaning Principle: Scrapers made of wear-resistant and corrosion-resistant materials like polyurethane or rubber are installed on the edge or bottom of the Conveyor Belt. During the operation of the conveyor belt, the scrapers are in close contact with the surface of the conveyor belt to scrape off materials and impurities on it, which then fall into a special collection device.
- Brush Cleaning Principle: Brush rollers with soft and wear-resistant bristles are installed above or below the conveyor belt. When the conveyor belt is running, the brush rollers rotate at a certain speed and come into contact with the surface of the conveyor belt, brushing off material particles, powder and other impurities.
- Air Flow Cleaning Principle: Air nozzles are arranged on both sides or above the Self Cleaning. When the Cleaning Conveyor Belt is in operation, the nozzles eject high-pressure air to form an air flow barrier or scouring effect, blowing off the dust, debris and other impurities on the conveyor belt.
- Cleaning Device: In addition to the basic conveying structure, Self Cleaning Conveyor Belt equipped with special automatic cleaning devices, such as scraper mechanisms, brush roller assemblies or air flow systems. These devices are precisely designed and installed to ensure effective contact with the conveyor belt surface and efficient removal of impurities.
- Conveyor Belt Material: Self Cleaning belt usually made of materials with good self-cleaning properties. Cleaning Conveyor Belt Manufacturers and Suppliers in China have good elasticity, wear resistance and corrosion resistance, and their smooth surface is not easy to adhere to materials. Plastic conveyor belts, such as those made of polyethylene or polypropylene, are light in weight, high in strength, have good chemical stability, and have a small friction coefficient, making it difficult for materials to adhere. Metal conveyor belts, including those made of stainless steel or carbon steel, have high strength, high temperature resistance and wear resistance, and their flat and non-deformable surfaces are also conducive to cleaning.
- Surface Texture: Some automatic cleaning conveyor belts have special surface textures. For example, patterned conveyor belts have patterns or protrusions such as herringbone or diamond patterns on their surfaces. These patterns can increase the friction between the conveyor belt and the materials to prevent slipping, and the gaps between the patterns can hold some material impurities, which will fall off under the action of gravity and centrifugal force as the conveyor belt rotates. Mesh conveyor belts, made by weaving metal or plastic wires into a mesh structure, have good air permeability and water permeability, allowing dust and impurities to fall through the mesh holes.