Oil-Resistant Conveyor Belts: Engineered for Durability in Demanding Environments
Oil-resistant conveyor belts are critical components in industries where exposure to oils, greases, or hydrocarbons is unavoidable. Designed to maintain structural integrity and operational efficiency, these belts ensure reliable material handling in sectors such as manufacturing, waste management, and energy production. Below, we explore three key product categories: Oil-Resistant Belts, Oil-Resistant Conveyor Belts, and Ordinary Oil-Resistant Conveyor Belts, highlighting their features, applications, and advantages.
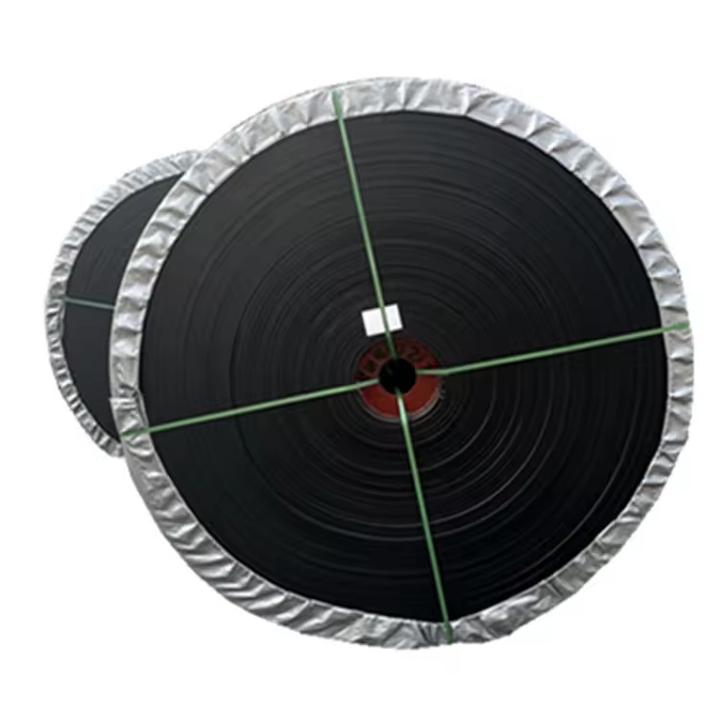
Description:
Oil Resistant Conveyor Belt are specialized rubber belts engineered with materials like Nitrile Rubber (NBR) or Neoprene to resist swelling, degradation, and mechanical wear caused by oil exposure. Ordinary oil resistant conveyor belt are ideal for applications involving frequent contact with petroleum-based products, hydraulic fluids, or lubricants.
2、Key Features:
Material: NBR or Neoprene compounds ensure excellent oil and fuel resistance.
Temperature Range: Operates effectively between -40°C to 120°C (-40°F to 248°F), suitable for both cold and high-heat environments.
Applications: Automotive assembly lines, hydraulic systems, and machinery requiring oil-resistant sealing or conveying.
Description:
Oil-resistant conveyor belts are heavy-duty solutions designed for industries like biomass energy, waste processing, and chemical plants. These belts combine oil resistance with flame-retardant properties for enhanced safety.